如何进行过程控制
本文介绍,通往防止缺陷之路开始于一个良好的过程品质计划。过程品质决定产品品质,其主要目标是限制和减少创造一个健康过程的变量。这个计划应该概述用于监测产品与过程的方法。
许多公司对产品缺陷发生率是被动反应的,虽然他们认为自己是前摄反应的,因为他们大多数的努力是去计数缺陷而不是检测过程。事实上,计数缺陷是被动反应的,因为损伤已经发生了。检测过程是比较前摄反应的,因为这是一个帮助防止缺陷的方法。的确,具有良好品质控制计划的公司正是要计数缺陷。但是更重要地,他们检测其过程和把注意力集中在缺陷的防止上。以下是讨论过程控制概念与工具、检测方法、和品质度量标准,从一个分成四种级别的品质计划开始:
预防行动与预防意识。过程在控制中还是失去控制。能够生产可接受的产品还是不能。如果是后者,则进行下三个级别的行动。
失效分析。有现成的技术与工具来有效地分析和调研典型的过程与产品问题
问题解决。有现成的结构性问题解决技术和工具(例如,因果关系图解、Pareto图表,等)来离析问题的根源。
改正行动。找到这些原因之后,可找到和实施永久的解决方法。
基本过程控制
过程控制将帮助达到和维持过程能力、稳定性和可重复性的一个所希望的水平。过程控制不只是统计;它是详细的一系列事件(表一)。如果遵循这些事件,那么过程控制将会达到。
表一、达到过程控制的典型的一系列事件
定义装配要求
建立装配过程
定义过程参数
定义过程品质计划
制作装配过程文件
制作过程品质计划文件
培训和给雇员授予合格证
开始有限的生产
收集特征与变量数据
计算过程能力
开始批量生产
继续数据收集
所有装配过程都有某些变量。统计过程控制(SPC,
statistical process control)提供工具来检测过程和监测变量,其中有两种形式:普通原因(common
cause)与特殊原因(special cause)(如Deming所定义的)。普通原因变量是在一个稳定的过程中固有的,即,虽然不完美,不管怎样一个稳定的过程是可重复的 - 检测的一个关键要求。相反,特殊原因变量是特殊行动的结果,如执行错误(即,制定成文件的过程没有遵循)。因此,除非一个过程是可重复的,结果(如在X条R图表上所显示的)将反应操作员的变化而不是过程变化。工程师脑子里总是想着过程失控的可能性,他们有时在检测它以防止得到低“分数”之前企图使过程表现完美。可是,这样一个步骤有一点弄巧成拙;统计过程控制(SPC)应该用来稳定新的过程和改进现有的过程。
最后,基本过程控制必须基于从精确测量与观察所获得的事实。控制图表,就是简单的以时间展开的柱状图,记录和显示数据。变量数据(如,胶点直径)是集中在过程上的和通过测量获得的,而特性数据是通过观察获得的和集中在产品上的。通常,收集与分析特性数据(attribute
data)是被动反应的行动,而收集与分析变量数据(variable
data)是更加积极性的步骤。
工具
过程控制依靠统计工具来测量、反馈和分析。众所周知的七个品质控制工具,是过程质量计划的必要部分,因为它们可用来收集、显示和分析数据。
检查表(check sheet),用于收集数据,也可显示数据。它们简单、容易应用,并有效地显示各种结果频率。
Pareto图表,在柱状图上以下降的顺序显示缺陷种类,对于把致命的少数从不重要的多数中分离出来是非常有用的。
因果关系图(cause-and-effect),将注意力集中在一个缺陷的最可能的原因和其潜在的相互联系性上面。注意力通常集中于四种类型:方法、材料、人员与设备。
流程图(flowchart),使用标准化的标识来说明过程中的各种步骤。一个流程图清晰地说明从开始到结束的整个装配过程。
柱状图(Histogram),是显示统计分布的条形/柱形图。它们在显示数据分散中有帮助,使得容易比较和分析。
散布图(scatter diagram),绘出无数的数据点来显示一个过程或产品的两个不同但又相关的特征之间的因果关系。
控制图(control chart),在时间上和在实际与强加德上/下极限之间,显示特性(计数的)或变量(测量的)数据。它们清楚地揭示可能影响过程能力的异常特性曲线、趋势和周期。有六种基本图形:
X bar - 显示一个测量系列的平均数的变化
R - 显示一个测量系列范围的变化
C - 显示缺陷数量的变化
U - 显示每个单元缺陷数量的变化
P - 显示缺陷比率的变化
Np - 显示确定单元数量的变化
检查
某个级别的产品检查是必要的和所希望的。可是,证据清楚地显示在长期运行中,大批量的检查不会改进产品质量。检查是一个筛选过程,尽力找出需要修理的不可接受的产品。大量检查应该避免,除非发生有必要100%产品筛选的事件。对于日常检查,应该基于一个合理的抽样计划。Deming经常提倡取消大批量的检查。相反,他鼓励统计上监测的稳健的和可重复的过程。
定义检查方法与工具是重要的。我们经常看到,人们知道怎样检查,结果多数建立其自己的方法,造成检查的变化。检查应该当作一个过程来定义,象任何其它过程一样制作出文件。一旦完成,检查员应该接受培训和发给合格证书。事实上,检查可分成三个基本模型:
当每个板上的每个元件都检查时(大批量检查)
当确认每个板上的特殊元件时(减少的批量检查)
当检查特殊板上的特殊元件时(抽样检查)
理想地,一个公司从第一种模型向最后一种模型进步。不幸的是,制造运作更容易从第一种模型开始,并停留在那里。印刷电路装配的复杂性影响检查,因为每个板的元件数量不断增加,造成更多困难来检查每个板上的每个元件。事实上,复杂性是批量检查不能改善产品质量的主要原因。一个方法是通过减少要检查的元件数量来减少检查的疲劳。理论上,可望马上检查出和修理所有的问题,实际上,这简直不可能。
焦点(focal point)检查是从上述模型中进步的一个例子。基于历史数据(即,Pareto图形分析),显示更高缺陷率的元件接受更频繁的检查。这个方法保证麻烦的元件得到更多的注意力。缺陷率低的元件更少检查或完全不检查,改善整个检查过程。
检查与监测
检查(inspection)是集中在产品上的;监测(monitoring)是集中在过程上的。一个良好的过程品质计划应该包括两者。可是,长期目标应该是更少检查和更多监测。这是所希望的,因为产品检查是被动性的(缺陷已经发生)而过程监测是积极性的(缺陷可以防止),这是一个价值增值概念。可是,更加困难的任务是建立一个不依靠批量检查的、平衡的检查与监测策略。
缺陷种类
缺陷代号,诸如锡桥、开路、少锡和元件丢失,用来简化数据收集与分析。在一个公司*,这些代号进一步分类成缺陷种类,指出需要另外改进的区域。一个饼图,如图一所示,是显示数据的有效方法。有四个缺陷种类:
过程能力(process capability),意味着过程不能达到所希望的结果。例如,一台不能持续产生所希望的胶点尺寸的滴胶机
过程执行(process execution),在这里过程是能够的,但整体执行差。例如,机器操作员没有跟随写下的操作规程。
缺陷材料(defective material),如密间距元件的引脚不能持续地满足共面性规格要求。
对可制造的设计(design for
manufacturability),意味着板不是设计成装配容易的。例如,基准点目标设计不正确。
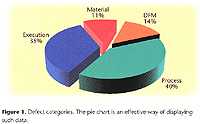
过程控制误区
误区 #1:过程控制与统计过程控制(SPC)是相同的。过程控制是一个概念;SPC是一套支持该概念的工具。在SPC可以成为一个有效的工具之前,过程必须稳定和可重复(但可能不是完美的)。
误区 #2:产生和显示图形图表是过程控制。只是为了给管理层和顾客一个映象的显示图表是浪费时间。使用图表来防止缺陷和解决问题才是过程控制的部分。
误区 #3:大批量检查(mass inspection)是一个有效的过程控制工具。批量检查不是过程控制。而它只是分类可接受与不可接受产品的一种企图。过程品质计划应该消除批量检查的需要。
检测的艺术
度量标准是检测表现的科学。例如,对于第一次通过合格率(FPY,
first-pass yield),一个度量标准揭示一个过程或运作的表现有多好,通常与所希望的结果或期望比较。因此,度量标准是重要的,因为一个公司必须具有检测其表现的能力。度量标准应该经常审查与分析 - 有些情况是每天,其它情况是每周。收集的信息不只是为管理层,而且应该与工程师、技术员、主管、操作员等共享。为了具有价值,度量标准必须基于事实和真正反映实际表现。在分析期间,管理层必须提高开发与真诚的气氛,不怕批评或惩罚。保证每个个人和班次使用相同的格式收集数据和事实上对其发现作出反应是非常重要的。
FPY 与
DPMO
如所提及的,一个经常使用的检测是第一次通过合格率(FPY)。传统上,表面贴装制造线的成功是以这个测量来评定的。运作的顺序通常是从锡膏印刷到在线测试(ICT),包括滴胶、元件贴装、回流焊接、通孔装配、波峰焊接、清洗和二次装配(压配的连接器、模压、增加其它元件、导线等)。FPY定义为印刷电路板(PCB)装配成功地完成的数量,除以所生产的装配总数。数学上表达为:FPY%
= [ 好板数 / 测试的板数> x 100 。
在有中至高复杂性板的一个典型的高混合的工厂,FPY范围可能在50~80%或者更高,取决于设备年龄和类型、检查方法、以及使用的过程控制技术。
FPY测量的一个问题是它只处理好板与坏板的数量;忽视了与坏板有联系的缺陷数量。当要调配资源来修理各种产品的现场问题时,这对高混合板制造商是一个关注。也可能具有一个似乎在第一次分析时可接受的FPY数,或许高于90%,而由于每个板有几个缺陷的一些板,返工与人力成本失去比例。例如,这个可能发生,如果贴装机器的送料器转换完成不正确,或者如果锡膏印刷在短期内不足够。虽然只是影响一些板,但在短期内产生的缺陷可能比每小时平均数高得多。
最近的趋势已经从把FPY作为一个方法到一个更现实的度量标准,叫做百万机会的缺陷数(DPMO,
defects per million opportunities)。对于这个度量,机会数等于零件(SMT或通孔)数加上焊接点数(只对元件,通路孔与测试点除外)。DPMO计算提供一个将缺陷按照板的复杂程度规范化的方法,即,对于相同的DPMO,机会较少的板将会有较少的缺陷,而具有多得多机会的高复杂性装配对于相同的DPMO将会有更多的缺陷(DPMO = [缺陷数 / 机会数> x 106)。与FPY的关系是反线性的:对一固定过程能力,随着机会数的增加,FPY将成比例地减少。
当在1999年第一次遇到这个度量时,我们决定在生产中选择一定数量的装配与实际的情况来测试该理论。有至少六个月生产历史的板是相当稳定的,数量上选择至少500或更多的单位。图二描述了该结果。所示的编号(P/N)以DPMO向右增加的图形显示与该理论的相关性。在这个例子中,工厂的平均DPMO在代表65%总量的20个产品的范围大约是55。在这个实际与理论之间关系的基础上,一些公司*已经转向把DPMO作为主要的表面贴装运作的度量标准。
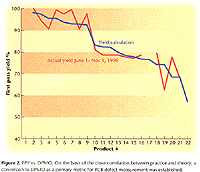
长期趋势 - 条形图(Bar chart)
在一个度量上沟通总趋势的一个方法是在时间上使用条形图,而不是在一个压缩的水平刻度上如图三所示。想法是要通过简单的条形来总结每年或每季度的数据,并在每月或每周的基础上显示更新的信息。以这种方法,该图表可以提供一个长期的数据,而更近期的数据可以一种提供临近的历史而不至于太忙方式显示出来。
例如,在一个特殊产品上,从图表得出的结论是:
2000年较早时期,DPMO低于目标(这样好)
然后,年中,发生一些事使得DPMO超过目标值
在改正行动之后,DPMO开始趋向于回到目标值
当然,可能对该问题有许多解释。可是,图表显示非常容易,在时间上、实际表现、以及注释,它可能是把结果向所有有关人员沟通的有力工具。
仪表板度量(Dashboard Metric)和品质之星(Quality Star)
检测性能表现是一件事情,有些地把数据和趋势通信给所有受影响的参与者,使他们可以使用数据,那绝对是另外一件事情。例如,“品质之星”方法由五个监测一个公司的健康和制造运作的基本度量组成。这些包括:
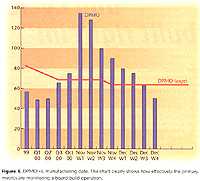
DPMO
到达产品的坏机(DOA, dead on
arrival products) - 在头三十天内不工作的产品(当顾客打开产品时)
保修失效 - 开始工作但在为了六个月期间的某个时候失效的,并返回修理的产品。
功能测试合格率 - 产品测试通过或不通过功能测试时的FPY计算。
质量审查 - 也是一个FPY计算 - 包括按照视觉标准,如
IPC-A-610 和内部工艺标准,检查的产品。
如果在所有这些方面性能表现良好,那么内部目标以及顾客对品质、可靠性、成本和性能的期望都应该满足。
品质之星的一个例子如图四所示(金色是“好”,蓝色是“坏”)。在微软的电子表格中的“雷达”曲线产生图表,并基于每个度量的一套满足的最低值和目标值。最低值应该产生一个有完全蓝色点的品质之星,如图四品质审查(quality
audit)所示。满足目标会产生一个完全金色的点的品质之星,如保修(warranty)、测试或DOA所示。部分满足目标将产生蓝色与金色的点的品质之星,如在DPMO度量标准中。例如,DPMO目标是65,如果满足,将找到如图四所示的充满品质之星的点。可是,如果实际结果是80(这比目标值差),那么将得到部分填充。
类似地,其它参数可设置到在图形上代表所希望的最小至目标性能的范围。一旦目标值与可接受性能的最低值传达给雇员,品质之星成为将每日、每周、每月、每季度或每年的性能数据通信给所有人的工具。
结论
质量改进,从一个计划、一套参照特殊标准的目标、测量的工具、一个作更好改变的方法、和一个通信结果的方式开始。本文概述了一个用来生产高品质PCB的品质系统的基本元素,和一个按照性能目标展示进度的、每个受影响的人员都可理解的方法。
|